Innovative Potted Insert for Sandwich Panels
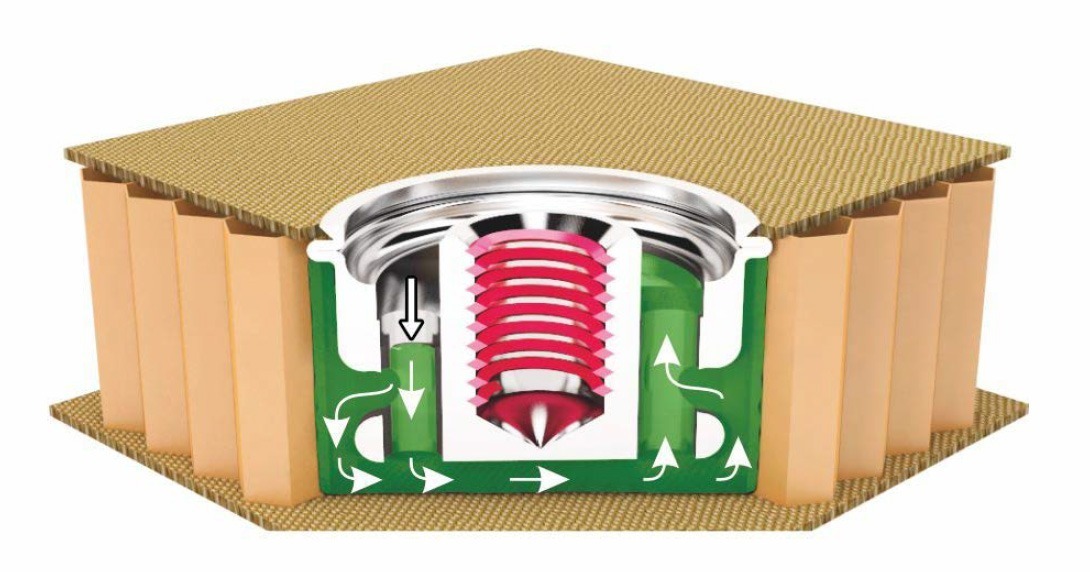
- Insert held in place by crimping operation
- Easy and reliable glue injection
- A visual inspection of the filling via the second vent hole
- No additional finishing operations

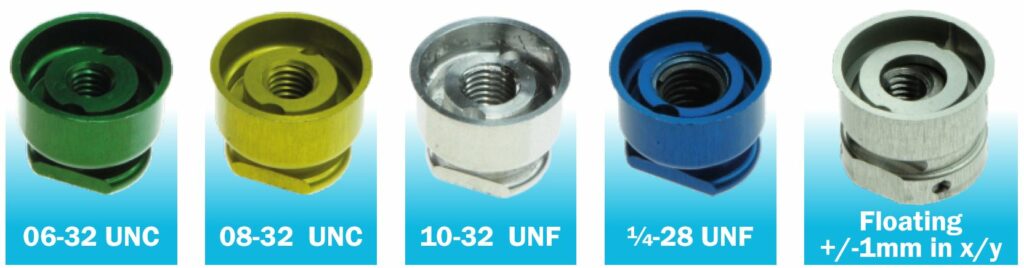
Démonstration SECAMnida (Composite Europe 2019)
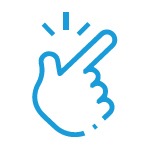
Simple
Immediate handling after crimping
No needs for finishing operations
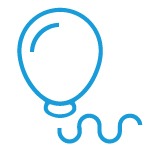
Light
50 % weight reduction
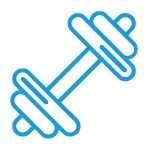
Strong
Higher mechanical strength
Pull-out 1800 N – Shear 3000 N
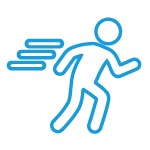
Fast
4 time quicker installation time
than conventional potted-in insert
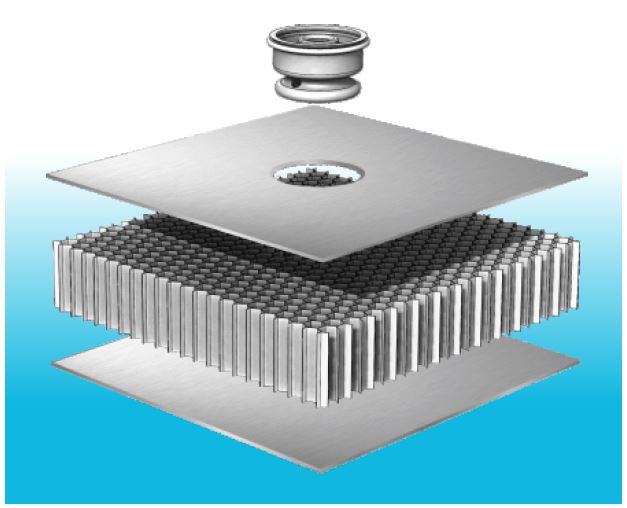
Types d’applications
- Total Panel Thickness : 8 to 40 mm
- Skin Thickness : 0,5 to 2 mm
- Insert Material : Aluminium or Stainless Steel
- Thread : M3 to M8 or Imperial
SECAMnida© is not just a potted insert for honeycomb sandwich panels.
Its highly reliable technology revolutionizes installation.
This fastening has a reinforced locking thread and is crimped onto the upper skin of the sandwich panel by deformation of the part. This effective anchoring permanently holds the insert in position and means the panel can be handled without risk, unlike the current inserts which are held in place simply by a self-adhesive “positioning” tab and which can tip in their hole before or during the potting operation.
After crimping, the two-component potting compound can then be injected,
and filling is accurately controlled by the filling indicator.
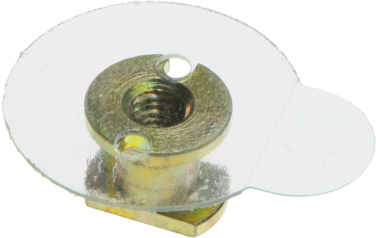

1
Drilling
2
Trimming
3
Tab Installation
4
Insert Installation
5
Injection
Curing Time
Tab removal
7
Finition
Handling
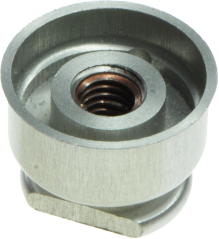

1
Drilling
2
Crimping
3
Injection
Curing Time
Handling
Whereas the current NAS inserts require seven operations to install them (drilling, trimming, etc.)
and immobilisation of almost 24 hours for full curing, the SECAMnida© insert offers unrivalled efficiency.
It is fitted in only three steps, reducing the installation time from two minutes to thirty seconds,
and the panel can be handled immediately to continue its manufacturing process.
AUTOMATION A SURE BET WITH GEBE2
The two industrialists began working together at the Paris-Le Bourget Air Show in 2019. Aware of the difficulties and costs linked to automating the installation of NAS-type potted inserts, GEBE2 was seeking a reliable, economical solution.
An exclusive partnership agreement was signed to progress beyond the idea stage and produce a demonstrator.
The study was launched and GEBE2 developed an all-in-one robotised effector able to drill, crimp, inject the potting compound and perform a fully automated final inspection.
The alliance between the two industrialists has led to a fully robotised solution for the installation of fastenings in all types of sandwich panel, both honeycomb and other.
It offers numerous advantages:
• Improved repeatability of the insert installation operation
• Automation of quality control
• Possibility to provide traceability of all the operations
• Versatility and adaptability of the system to the geometries of complex parts
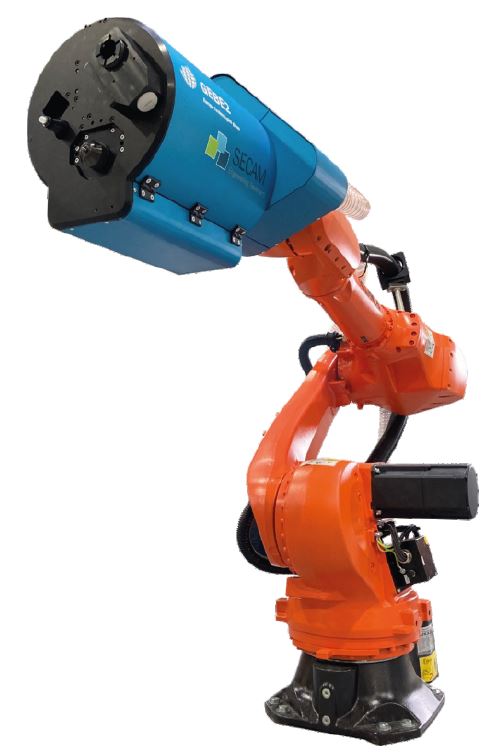
These products may also be of interest to you
A standard range of bondable inserts
A standard range of bondable inserts
SECAMnida® : la fixation industrielle innovante pour panneaux sandwich
SECAMnida® is a high-performance fastening solution specifically designed for honeycomb sandwich panels. Thanks to its reliable crimping technology and compatibility with two-component adhesives, it optimizes the installation of threaded inserts in complex industrial environments. This innovative solution meets the highest standards in the aerospace, railway, and automotive sectors.
A solution three times faster than a standard potted insert
Installing a SECAMnida® insert requires only three steps (drilling, crimping, injection), compared to seven for a traditional NAS insert. Thanks to its unique design, the insert can be immediately handled after crimping, with no risk of shifting. Installation time is reduced from 2 minutes to 30 seconds, providing a significant productivity boost.
Technical performance and industrial advantages
- Simplicity: Immediate handling after installation
- Lightweight: Up to 50% lighter than other systems
- Strength: Pull-out strength > 1800 N, Shear strength > 3000 N
- Reliability: No finishing required after adhesive curing
With SECAMnida®, adhesive fill is precisely controlled thanks to a built-in visual indicator, ensuring maximum production safety.
Multi-sector and custom applications
Designed for sandwich panels with a thickness of 8 to 40 mm and skin thickness from 0.5 to 2 mm, SECAMnida® is compatible with numerous materials (aluminum, stainless steel, steel) and threads (M3 to M8, imperial).
Thanks to its patented technology, SECAMnida® exceeds industry standards and is perfectly suited for demanding applications in:
- Aerospace (interior shells, lightweight fastenings)
- Railway (technical panels, interior fittings)
- Transport and energy industries (composite panels)
Simplified installation process
Method comparison
Traditional inserts require multiple complex steps: drilling, routing, positioning via adhesive tabs, injecting, drying, removing accessories, finishing… so many operations that generate variability and cost.
SECAMnida® enables:
- Standard drilling
- Direct cold-form crimping of the insert
- Reliable and uniform adhesive injection
The result: a clean, fast, safe, and fully repeatable installation.
Partnership with GEBE2: toward industrial automation
In 2019, at the Paris Air Show, SECAM partnered with GEBE2, an expert in industrial robotics. Together, they developed a robotic cell capable of automatically drilling, crimping, injecting, and inspecting the installation of fasteners in all types of sandwich panels.
This automation solution offers:
- Greater repeatability of installations
- Automated quality control
- Complete traceability of operations
- Adaptability to complex geometries
This development is part of SECAM Fixation’s mission to industrialize its solutions and support clients in achieving operational excellence.
Why choose SECAMnida® over a NAS insert?
Unlike NAS inserts, which are typically secured with fragile adhesive tabs, SECAMnida® ensures mechanical retention right from installation. The insert remains stable even if manipulated before adhesive curing, offering a major advantage in terms of safety, reliability, and efficiency.
Additionally, the integrated fill indicator provides an immediate visual check of the proper two-component adhesive fill, reducing defects and production waste.
Need a custom project?
SECAM fastening solutions are available in standard versions or tailored to specifications. Our in-house engineering office supports you in analyzing your needs and designing custom fasteners adapted to your constraints (mechanical resistance, lifecycle, production rate…).
For any quote or sample request, please contact our team.
Discover complementary products
- SECAM Autofix® – Bonded fastener with fill indicator
- S-Plate Composite Fasteners – Standard bonded inserts
- SECAMnida® 2024 – New generation of crimp-in inserts
Contact us
Do you have a technical or commercial question?
Leave us your contact details so we can get back to you.
You can also write to us or call us.
FAQ - SECAMnida: Innovative industrial fastening system for sandwich panels
What is SECAMnida®?
SECAMnida® is an innovative fastening solution designed for honeycomb sandwich panels. It enables fast, reliable, and durable installation thanks to a mechanical crimping system and a patented visual fill indicator. This solution optimizes mechanical performance while reducing installation time.
What are the advantages of crimping with SECAMnida®?
Crimping ensures immediate and secure anchoring of the insert into the panel skin, with no risk of tilting before or during adhesive injection. It replaces fragile adhesive tabs used in traditional inserts, improves assembly reliability, and allows immediate handling of the panel after installation.
Which materials are compatible with SECAMnida®?
SECAMnida® is compatible with sandwich panels featuring skins made of aluminum, stainless steel, or steel. It supports panel thicknesses from 8 to 40 mm and skin thicknesses from 0.5 to 2 mm. It is ideal for applications in aerospace, rail, and automotive sectors.
How is SECAMnida® installed?
Installation involves three simple steps:
- Panel drilling
- Cold-form crimping of the insert
- Two-component adhesive injection up to the visual fill indicator
This process replaces the 7 steps required for NAS inserts and reduces installation time by a factor of four.
What are the benefits for industrial production?
With its fast installation (30 seconds), immediate handling, and visual fill control, SECAMnida® improves productivity, quality, and traceability. The process can also be fully automated using robotics developed in partnership with GEBE2.
Can SECAMnida® be installed automatically?
Yes. SECAM and GEBE2 have co-developed a robotic system capable of drilling, crimping, injecting, and controlling each step of the process. It ensures high repeatability, automated quality control, and full traceability in industrial settings.
How can I verify correct adhesive filling?
SECAMnida® features a patented visual indicator that clearly shows the fill level of the adhesive inside the panel. This guarantees a complete fill and prevents bonding issues, ensuring high-quality and consistent assemblies.
What alternatives exist to SECAMnida®?
SECAM also offers other fastening solutions for composites and sandwich panels:
- SECAM Autofix® – Bonded fastener with fill indicator
- S-Plate – Standard range of bonded inserts
For tailored support, feel free to contact our team.